Soft drinks, also known as non-carbonated beverages, have been gaining ground in the beverage market, conquering the taste of consumers looking for refreshing options and more subtle flavors. At MachinePoint, we specialize in the commercialization of used soft drink production line. Our approach is based on providing integral solutions for each stage of the manufacturing process by offering specialized used equipment.
In the early days, non-carbonated soft drinks, such as juices and nectars, were the most common options available for quenching thirst and enjoying natural flavors. The presence of these non-carbonated beverages was linked to the availability of local fruits and flavors, which were usually prepared by hand or in small productions.
Over time, the rise of carbonated soft drinks has captured the public’s attention with their bubbles and effervescence, leading to greater industrialization and commercialization of carbonated beverages. However, in a more contemporary scenario, consumer demand has been evolving, and the search for healthier, less carbonated alternatives has led to a resurgence of non-carbonated soft drinks.
Today, the non-carbonated beverage manufacturing process has undergone significant technological advances and efficiency improvements, allowing these beverages to be produced on a larger scale and with a wider variety of flavors. At MachinePoint, we offer a wide range of used machinery that facilitates this production process, from accurate flavor mixing to efficient beverage packaging.
Which is the process of making non-carbonated beverages?
The process of manufacturing still beverages consists of several steps. First, the ingredients, which include fruit or flavor concentrates, de-aerated water and sugar, are prepared. They are then blended in appropriate proportions and the sugar is dissolved in water. The mixture is homogenized to ensure even distribution of flavors.
In some cases, additional processes such as pasteurization or microfiltration are carried out to ensure the safety and shelf life of the product. The beverage is then packaged, labeled and packed in boxes or packs. Finally, the packs are palletized and wrapped with plastic film for transport and storage.
What machinery can MachinePoint provide me with for a non-carbonated beverage line?
In a soft drink production line, it is essential to have a variety of specialized equipment for each stage of the process. At MachinePoint, as experts in buying and selling used machinery, we can provide you with all the necessary equipment for your soft drink plant. From blending systems to obtain the perfect combination of flavors, to sugar dissolving machines and homogenizers that guarantee a uniform and high quality mix.
We also offer pasteurizers and aseptic processing to ensure microbiological product safety. Our heat exchangers and other heat treatment machines precisely control the temperature during processing. In addition, we have blowers, compressors, rinsers, fillers, cappers, labelers, packers, stretch wrappers, palletizers and pallet wrappers to complete your production line efficiently and effectively. With our experience and wide selection of used machinery, we are ready to meet your needs and help you boost your non-carbonated beverage business.
As a general rule a typical soft drink plant can include the following equipment:
- Mixing and Blending Units
- Storage Units
- Sugar dissolving machines
- Homogenizer
- Pasteurizers
- Dosing machines
- Aseptic processing
- Heat exchangers or other heat treatment machines
- CIP & SIP
- Clarification machines
- Extracting line – if juice extracted directly from fresh fruit or vegetables
- Blowmoulding machine and compressors
- Rinser, Filler and Capper
- Labelling machine
- Packer
- Shrink Wrapper
- Palletizer
- Pallet wrapper
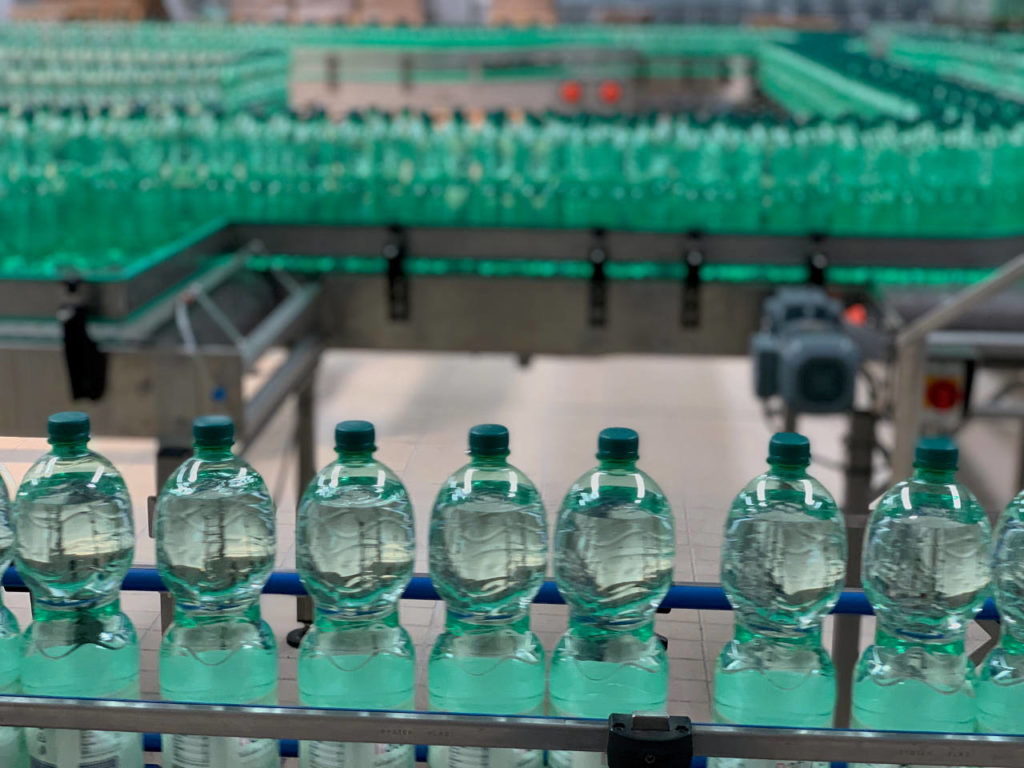
How to improve the efficiency of non-carbonated soft drink production lines
In the beverage industry, improving efficiency in production lines is crucial to remaining competitive in the market. Particularly in the non-carbonated soft drinks sector, optimizing production efficiency is essential to meeting consumer needs and ensuring profitability.
One of the key strategies for improving efficiency in still soft drink production lines is the implementation of advanced technology. Real-time monitoring systems and Manufacturing Execution Systems (MES) are powerful tools for collecting real-time data and providing a comprehensive view of line performance. These systems make it possible to quickly identify any inefficiencies, such as unplanned stops, extended downtime or product quality issues.
In addition, optimizing workflow and eliminating any bottlenecks are essential elements for improving efficiency on production lines. Analyzing and adjusting production processes, from raw material supply to final packaging, helps to minimize changeover times, reduce waste and streamline overall production.
Employee training and engagement also play a key role in improving efficiency. Providing appropriate training programs and fostering a collaborative work environment focused on continuous improvement helps maximize line performance and make the most of available resources.
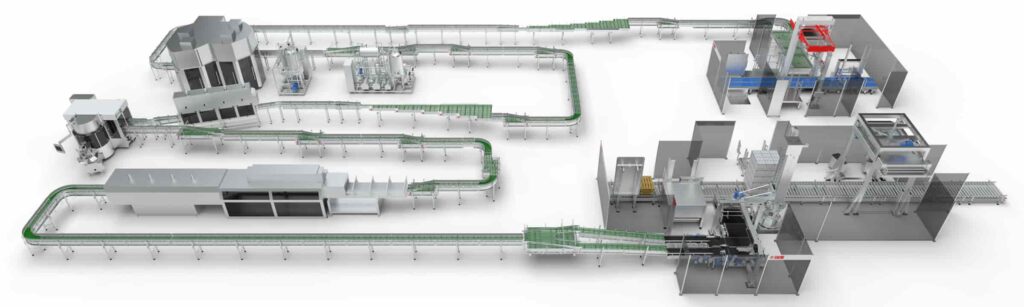